Cnc Threading Machine
THREADING ON CNC LATHES
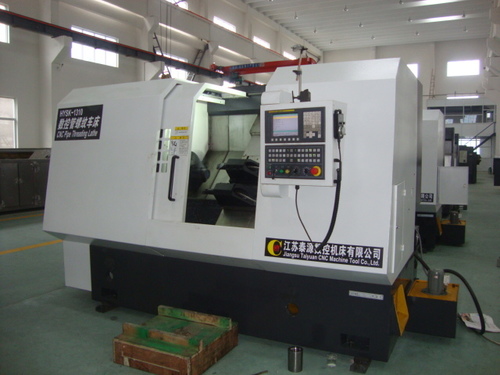
CNC pipe threading machine is widely used CNC machine tool for pipe threading work which is mainly designed not only for threading of pipe work in petroleum industry but also for the turning of pipe threads of various kinds like cylindrical and conical threads and end-face threads as well. Quick info on CNC Tapping including tap holders, tap collets, tapping attachments, rigid tapping, feeds & speeds, and more. Cutting Threads: Tapping, Single Point Threading, and Thread Milling. There are a variety of ways to make threads on CNC Machines, namely by tapping, single point threading, and by thread milling. Each one has pros. Alibaba.com offers 3,998 cnc pipe threading machine products. About 4% of these are thread rolling machines, 1% are other metal & metallurgy machinery. A wide variety of cnc pipe threading machine options are available to you, such as free samples, paid samples. China Pipe Threading Machine manufacturers - Select 2019 high quality Pipe Threading Machine products in best price from certified Chinese Machine Dryer manufacturers, Finishing Machine suppliers, wholesalers and factory on Made-in-China.com. Alibaba.com offers 3,998 cnc pipe threading machine products. About 4% of these are thread rolling machines, 1% are other metal & metallurgy machinery. A wide variety of cnc pipe threading machine options are available to you, such as free samples, paid samples.
CNC lathes can produce a very high quality thread in addition to the variety of turning and boring operations, in a single setup of the machined part. This is a very attractive feature for manufacturers and many machine shops have purchased a CNC lathe for that reason along. Any secondary operation requires additional setup, increasing the cost of production.
Single point thread cutting - typically known as a single point threading - uses a tool holder similar to other tool holders, but contains one special threading indexable insert, which may have one, two or three tips. Generally, the shape and size of the threading insert must correspond to the shape and size of the finished thread - Figure 38-1.
Figure 38-1: Comparison of the thread form and the threading tool shape
By definition, a single point threading is a machining process of cutting a helical groove of a specific shape with a uniform advancement per spindle revolution. The shape or form of the thread is mainly determined by the shape and mounting position of the cutting tool. The uniformity of advancement is controlled by the programmed feedrate.
Form of a Thread
The most common thread form used in CNC programming is the familiar V-thread (in the shape of the letter V) with a 60 included angle. There is a large variety of the V-shape forms in manufacturing, including metric and English threads. Other forms include trapezoidal shapes such as metric trapezoid, ACME and worm..
Read Next
Thread rolling delivers consistent results on workpieces. Imagine grinding the most optimum profile possible on a cutting tool. Once it touches metal, it starts to wear. With thread rolling, hardened dies are used, which press onto the material causing it to plastically deform to the dies' mirror image.
Every time the dies roll a thread, they gain stress. The stress builds up to a point that the material of the dies just gives up--fatiguing. Until the dies fail, the same profile will be produced with no adjustments of the head.
Featured Content
Here's how to capitalize on the inherent consistency of thread rolling.
A Brief Review
Axial thread rolling does its work by moving from the front (tailstock) of the part along the spindle centerline. In a single pass, three (up to six) rollers, synchronized by a planetary gear system, impart the desired OD thread shape, depth and pitch onto a workpiece. Generally, the rotation of the workpiece rotates the rollers. For CNC turning applications, a thread rolling head is usually placed in the tool turret.
The thread form on axial rolls consists of straight annular rings that are ground to the pitch of the thread to be produced. The rolls are positioned in the head at a skew angle that is approximate to the thread's helical (lead) angle.
Because of the skew angle, both sides of the rolls can be used. The skew angle also produces a forward motion, making the roller head self-feeding and self-opening. Because it traverses the workpiece, an axial head can produce threads that are longer than itself.
Pick A Thread
Current capacities for axial thread rolling heads range from 0.06 to 9 inches in diameter. Besides standard 60-degree profiles, acme, buttress, knuckle, knurls, splines, special profiles and burnishing are possible.
Like the chamfer on a tap, the beginning of the thread roll is progressive. If the first ring on the axial roll were full profile, it would do all the work. More progressive rings are generally recommended for optimum roll life.
A shorter progression can be used to allow threading up closer to a shoulder, but roll life will be adversely affected. Standard leads are expressed as 2K, 1K and 0.6 K. The numbers indicate how many annular rings are progressive. About the closest that an axial system can thread to a shoulder is 11/2 times pitch, which equates to a 0.6K lead.
CNC Machine Parameters
Thread roll heads have ranges of operations. Larger thread heads have larger ranges of operations. Taking advantage of the best efficiency available from a thread roll means considering several pertinent parameters.
We'll step through these parameters. For simplicity, we'll describe the use of a Fette F2 axial head, as our example, producing a ½-13, UNC 2A thread approximately three inches long. It has a threading range of 5/16 to 5/8 inch.
- Horsepower--In general, if the roll threading head can fit on the machine, there's enough horsepower. Where it is still questionable, a formula has been developed that can provide a minimum horsepower estimate. It's based on our ½-13 example using 4140 steel (28-34 Rc):
(1.037 × 10-6) × T × P × D × S = horsepower
Where:
Constant = (1.037 × 10-6)
T = material tensile strength = 125,000 psi
P = thread pitch (1/13) = 0.077'
D = nominal thread diameter = 0.50'
S = spindle speed = 917 rpm (120 sfm)
(1.037 × 10-6) × 125,000 × 0.077 × 0.500 × 917 = 4.6 hp
To find out if there is sufficient torque, apply this formula:
5250 × hp = torque (ft/lbs)
rpm
Where:
Constant = 5250
hp = 4.6
rpm = 917 (120 sfm)
5250 × 4.6 = 26.3 ft/lbs
917
It should be noted that these values are approximate and in most cases actual operational results are less.
- Cycle Time--Axial thread rolling times can be calculated with a single formula:
60 × L = time (seconds)
P × rpm
Where:
Constant = 60
L = length = 3'
P = thread's pitch (1/13) = 0.077'
rpm = 917
60 × 3 = 2.5 sec
0.077 × 917
- Speeds--For most axial systems, suggested speeds are from 60 to 300 sfm. That's not very specific. Realistically, a speed of 100 to 150 sfm should cover the majority of applications. We've used 120 sfm in our example.
There is a simple method of optimizing thread rolling speed for a lathe. The least amount of spindle load means the material is flowing with the least resistance. Using the spindle load meter built into most CNC turning centers, the best rpm for an application can be determined.
Start a thread rolling project around 100 to 120 sfm and increase the speed in 50 to 100 rpm increments. Watch for the speed point that produces the least amount of load. This will be the optimum rpm for the application, automatically taking into account material, hardness, diameter, pitch, head size and horsepower.
- Feeds--Because the axial system uses straight annular rings positioned in the head at a skew angle, heads are self-feeding--one thread pitch per revolution. For our (1/2-13) thread, that's 0.0769 ipr (inches per revolution).
But because the head is self-feeding, a feed rate approximately 0.001 to 0.002 inch less than pitch can compensate for the material's elongation and helps to provide optimum roll life. More optimum results will be obtained by feeding the thread rolling head at 0.075 ipr. - Thread Length--An exception to the above rule comes when combining the thread's pitch and length with the head's opening distance. In other words, allowance for the head's opening distance is needed or it opens before the end of the stroke.
Our F2 has an opening distance of 0.120 inch. Using 0.002 inch under pitch as a feed rate (0.075 ipr), we can produce approximately 60 threads before the head opens--0.120/0.002=60.
Therefore, maximum length of thread at 0.002 inch less than pitch (60 x 0.075 inch), would be 4.5 inches. If you need a thread 4.75 inches long, well, you see the problem.
Cnc Machine Threading Calculation
In this case, should the thread's length be longer than 4.5 inches, then a feed of 0.001 inch less than pitch (0.076 ipr) will give you approximately nine inches of thread length capability.
If your thread length is greater than nine inches, just feed under pitch for a couple of inches, then feed at pitch for the balance of the thread's length. You've still built in a 'float' for self-feeding, and the CNC's capabilities make it easy to do.
To actuate the opening of the head, program a 0.5-second dwell at the end of the Z-axis travel. This will allow the front-end assembly to self-feed forward enough to disengage the rollers--creating clearance between the rolls and the threaded part--hence opening the head.
Workpiece Parameters
Thread rolling is applied on a large variety of workpiece materials and configurations. The cold forming process doesn't remove stock to make a thread, it rearranges it instead. Therefore, turning the stock material to correct blank diameter is important for getting accurate results.
- Blank Diameter--The majority of thread profiles are symmetrical so that the distance above the pitch line is equal to the distance below the pitch line. Because the volume of material in each area is the same, the starting blank diameter is approximately equal to the pitch diameter of the thread to be rolled.
Here's a reference equation you can use for 60-degree form threads:
Nominal diameter - (0.72 × Pitch) = starting blank diameter (a reference)
Where:
Constant = 0.72
Nominal diameter = 0.50' (equals OD with no allowances subtracted)
Pitch = 1/13 = 0.077'
0.50-(0.72 × 0.077') = 0.464' (starting blank diameter reference)
Most of the material that is displaced below the pitch line will flow above the pitch line. However, some of the material will be compressed and some will elongate. This calculation is for reference only.
The final blank diameter will be determined after adjusting the thread rolling head to produce the part's final pitch diameter. Changes can then be made to the blank diameter to produce the part's nominal diameter.
Because the area along the pitch line of the thread is greater than the area at the crest of the thread, a change in blank diameter will have a greater effect on the major diameter. The ratio of blank diameter to major diameter is approximately 1:3.
- Blank diameter tolerance--Using the 1:3 ratio, blank diameter tolerance then could equal approximately one-third of the thread's major diameter tolerance. A good rule of thumb is that the blank diameter's tolerance should not be more than half of the thread's pitch diameter tolerance.
- Chamfer angle--A common mistake in thread rolling is starting with an angle on the pre-rolled blank that is the same as the angle to be produced on the finished part. Like the blank diameter, the pre-rolled chamfer angle will be altered by the displacement of material during the thread rolling process.
A pre-rolled chamfer angle will change by approximately 15 degrees from the center line of the part. For example, a 30-degree angle will be displaced outward to approximately 45 degrees.
Pre-rolled chamfer angles of 10 to 30 degrees from the part center line are recommended. For stronger workpiece materials and coarser pitches, smaller angles of 10 to 20 degrees should be used.
With a chamfer angle above 30 degrees, the displaced material will be forced against the thread roll's leading flank. The side force, which is not on the supported trailing flank, will shorten roll life and can cause damage to the thread rolls.
The chamfer angle starting diameter is also critical. For the axial system, it should be half of one tooth height ( approximately 0.020 to 0.040 inch) less than the thread's minor diameter. If the starting diameter of the chamfer angle is too big, some material will flow forward and cause the face of the part to become concave. This condition can be detrimental to thread roll life.
- Undercut--Undercut or not, the same pre-roll chamfer recommendations should be followed. An undercut is not necessary for the rolling operation, as long as the thread runout can be accommodated by the mating part. If the part has an undercut, the starting diameter of the chamfer angle must be less than the minor diameter of the final thread, or the rolls will leave marks in this area.
Roller Adjustment
Typically, two methods of roller adjustment are used: either an accurate threaded part or a plug gage (turned diameter) that has a diameter equal to the thread's root or minor diameter. Place this between the rolls and 'close' them down until they make contact. This will be an initial setting.
Please appreciate that the roller forces will be greater than your hand-tight initial setting. You can assume that the rolls will need to be adjusted slightly smaller--one-half to one mark in the negative direction on the calibration scale.
It's important to understand that where the rolls are set produces the thread's root (minor) diameter and the flank angles. The flank angles, in turn, will mathematically provide the thread's pitch diameter.
The amount of material that we displace on the 'blank diameter' will produce the thread's final outside or major diameter. The point is to adjust the rolls first for pitch diameter. (You should worry about the major diameter later.) After the first test part is measured, any further adjustments of the setting should be small--less than one-quarter of a mark on the calibration dial.
Place the pre-adjusted head in the machine's turret, move to X-axis zero and jog the open thread rolls, in Z-axis, over the blank diameter. Move the turret/head forward until the face of the rolls are where you want the thread to end.
Here's a hint: If there's a shoulder involved, close the head/rolls down onto the blank diameter. Open the head slightly, and by rotating one roll, move it forward on the Z-axis until the roll stops--you've hit the shoulder. Reference this position on the control and back up 0.005 to 0.020 inch. Reference this position on the control and input it as the end of Z-axis travel. You've fooled the machine.
When you come off the part, and close the head, the front end assembly will physically move back a fixed amount (depending on head size and manufacturer). In operation, when the head is at the end of the Z-axis travel, it will shop short by this fixed amount. With a 1/2- to 1-second dwell programmed at the end of the Z-axis stroke, the front end assembly will self-feed forward and self-open at the position previously set.
While in this position, let's do what I call a 'quick check' for alignment. Manually close the head/rolls down onto the blank. If we have good alignment, all three rolls will contact the blank diameter at about the same time. By rotating the rolls, try to find the first and last roll that makes contact.
Now make a judgment call. This method will provide you with an idea of the head's alignment and the direction of any misalignment. The final objective is to get the rollers in position on a correctly sized blank to produce the specified thread size and quality.
Host Jira Software on your server for more customization and control. Download and try Jira Software Server free for 30 days. Jira app download. Mobile for Jira Enterprise for Android is the ultimate solution to use Atlassian Jira on your Android device. It works with Jira core, Jira software and Jira service desk. Open links directly in the app (for Jira 8.4 and later) To help you navigate between pages, you can go directly from a link, for example in an email notification, to the app. If you do not have the app yet, clicking the link will take you to the app download page in Play store (only for Android). Jira mobile enables software and service desk teams to keep work moving from anywhere. Download the app today for free on iPhone, iPad, or Android.
Auto-Closing
As we've seen, a thread roller opens automatically at a calculated point in its stroke. Automatic closing can usually be done within the normal cycle of the machine. Unfortunately, differences in CNC machines make it difficult to provide a single closing method. Axial heads typically have a handle that can be used to manually close the head. This handle, or an adaptation of, can be used to automatically close the head.
For example, the head can be positioned so a standard turret index swipes the handle past a fixed object like the lower way cover, a second turret, tailstock, bracket, and so on, thus closing the head automatically.
Programming
A programming sample has been written for rolling our ½-13 thread, 3 inches long, located in station 8 on the turret. After the thread is rolled, we index to station 10 and move the head against a pre-positioned angle bracket to reset (close) the head.
In Closing
A good manufacturer of thread-rolling heads should provide capable technical support not only for their equipment, but also suggestions for your application. It's equally important that you provide your thread rolling equipment manufacturer with as much job detail as possible, namely: part print, material (including hardness if over 30 Rc), quantities, machine tool, operation, bar stock, chucker, tailstock and/or between centers. As with cutting, there are different methods used in thread rolling. Which system is best depends mainly on the above factors.
Play Adventure Quest to explore an online RPG and other web browser games for free with no software to download. New adventures built in Flash every week. Embark on an epic quest to save world in League of Angels III, the latest entry in the free-to-play browser-based MMORPG franchise. Embark on an epic tale of glory in The Third Age, a free-to-play browser MMORPG from R2 Games that evokes images of the most legendary of all fantasy worlds.